Case Study: Transforming a Veszprem Factory with Advanced Process Control Software
Introduction to Advanced Process Control Software
In today's rapidly evolving industrial landscape, the integration of technology into manufacturing processes is crucial for enhancing efficiency, productivity, and competitiveness. **Advanced Process Control (APC) software** plays a pivotal role in transforming traditional factories into modern, efficient production units. In this case study, we explore how a factory in Veszprem underwent a significant transformation by implementing APC software.
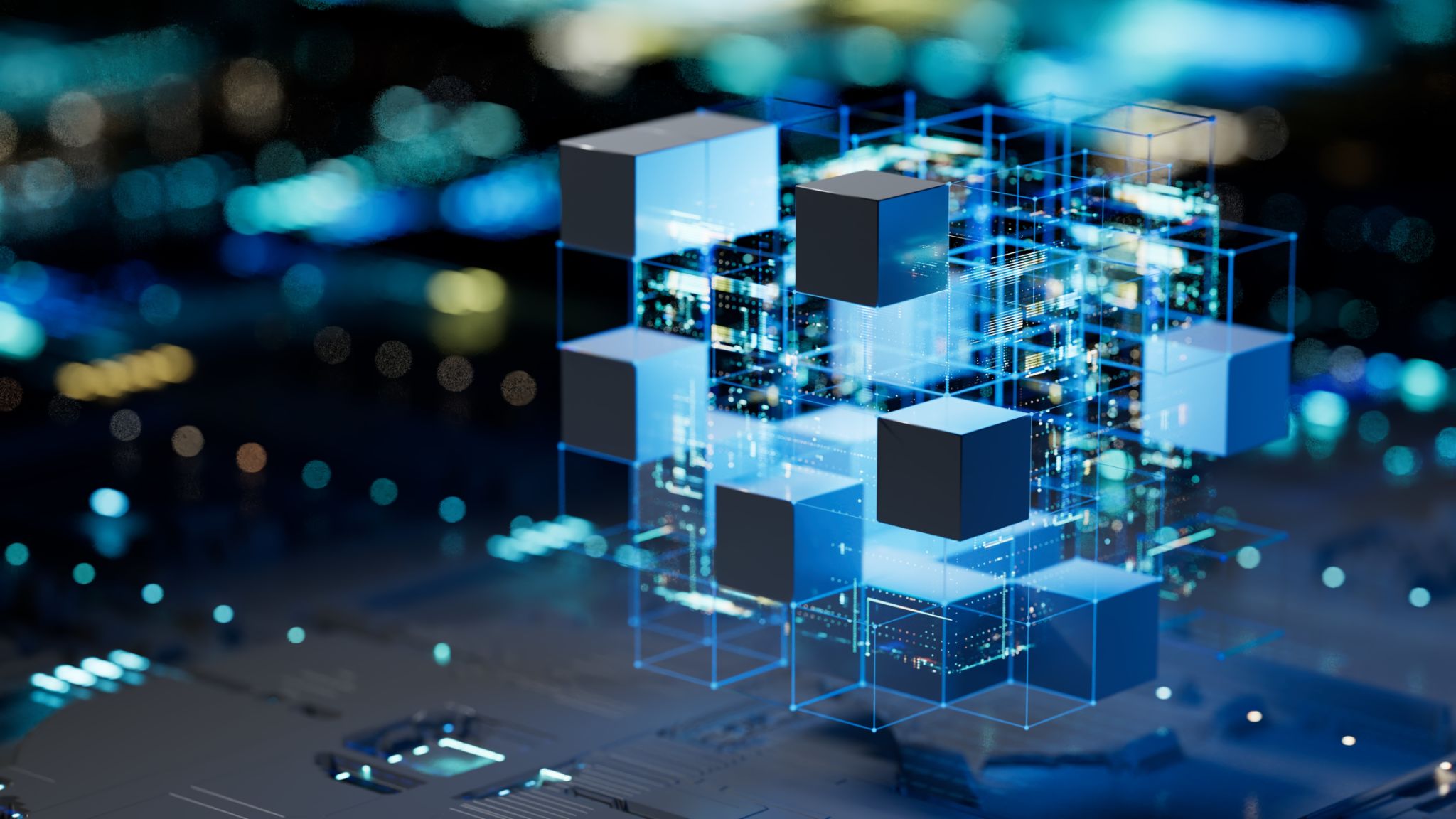
Background of the Veszprem Factory
The Veszprem factory, a long-standing player in the manufacturing sector, was facing challenges typical of traditional production facilities. These included inconsistent product quality, inefficient energy usage, and high operational costs. The management recognized the need for a technological upgrade to remain competitive in the market.
After extensive research and consultation with industry experts, the decision was made to adopt Advanced Process Control software. This decision was driven by the software's potential to optimize processes, reduce waste, and improve overall operational efficiency.
Implementation Process
The implementation of APC software in the Veszprem factory was a multi-phase project. The process began with a thorough analysis of existing operations to identify key areas that required optimization. This was followed by the customization of the software to meet the specific needs of the factory.
- Initial Assessment: Conducting a comprehensive review of current processes.
- Customization: Tailoring the software features to fit factory requirements.
- Integration: Seamlessly incorporating the software into daily operations.
- Training: Providing hands-on training to staff and management.
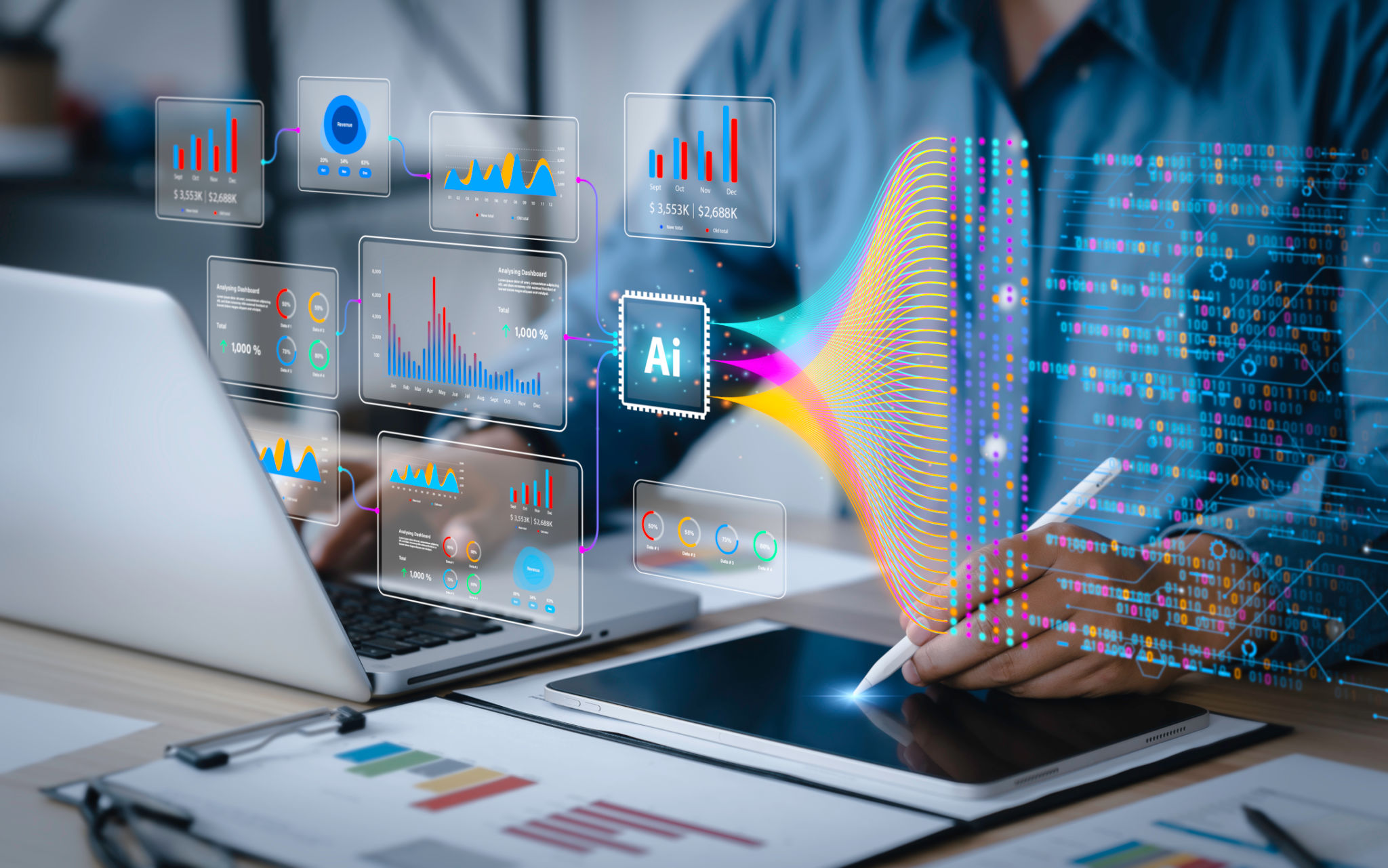
Benefits Realized
The integration of APC software brought about numerous benefits for the Veszprem factory. Key improvements included:
- Enhanced Product Quality: Consistent quality control mechanisms reduced variability and improved product standards.
- Energy Efficiency: Optimized processes led to a significant reduction in energy consumption.
- Cost Reduction: Operational costs decreased due to minimized waste and streamlined processes.
Challenges Faced
Despite the success, the journey was not without its challenges. The primary hurdle was resistance to change among employees accustomed to traditional methods. Overcoming this required effective communication and demonstrating the tangible benefits of the new system.
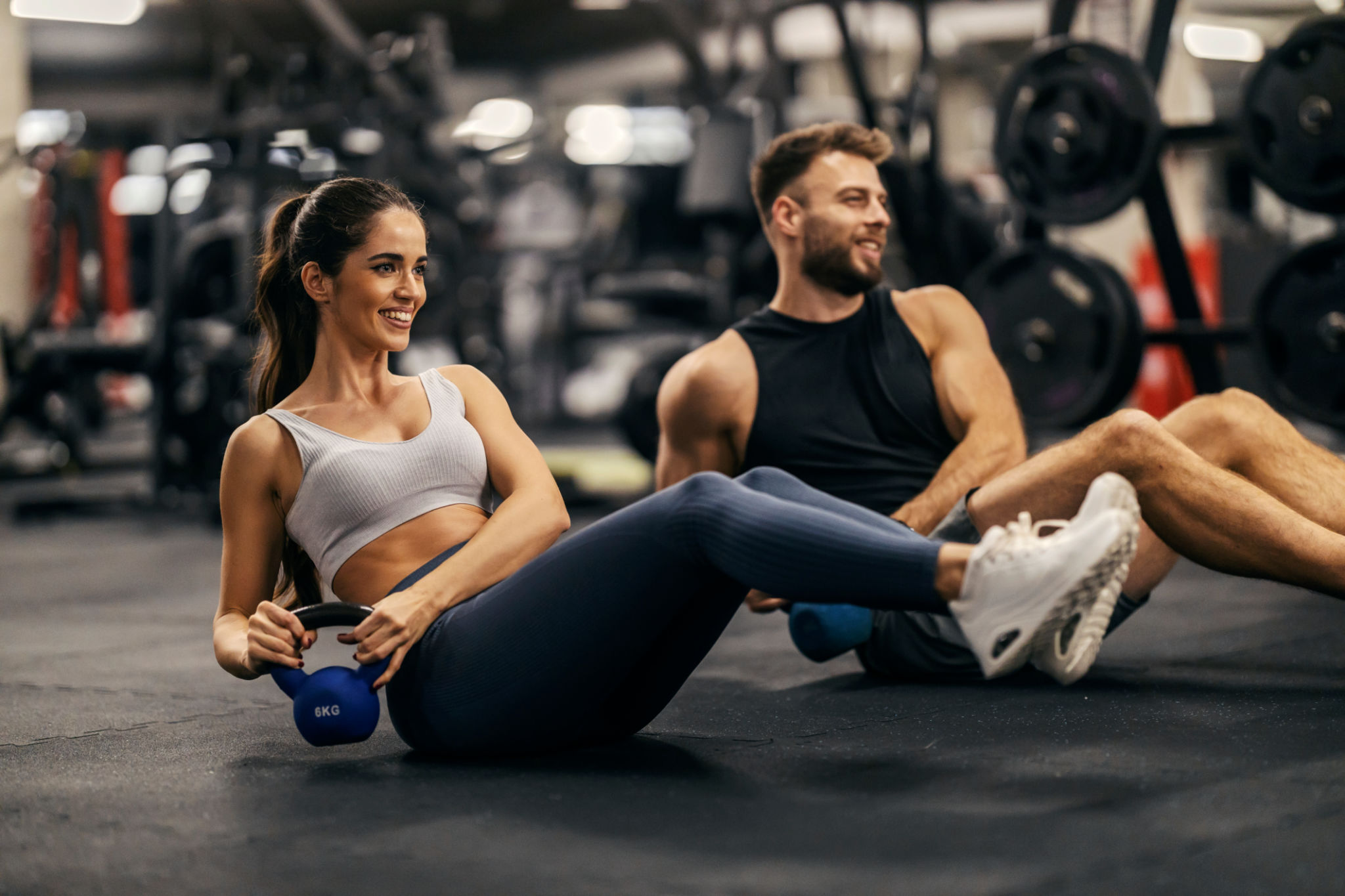
Another challenge was ensuring seamless integration with existing machinery and systems. This necessitated a phased approach to implementation, allowing for adjustments and troubleshooting without disrupting production.
Conclusion: A Model for Future Transformations
The transformation of the Veszprem factory through Advanced Process Control software serves as an inspiring example for other manufacturing facilities considering technological upgrades. The success story highlights the importance of strategic planning, employee involvement, and continuous improvement.
As industries continue to evolve, embracing such advancements is essential for maintaining competitiveness and achieving long-term sustainability. The Veszprem factory's journey underscores how innovation can pave the way for enhanced efficiency and productivity in manufacturing.