Expert Tips on Enhancing Factory Efficiency with Control Software
Understanding the Role of Control Software in Factories
In today's rapidly advancing industrial landscape, factories are increasingly turning to control software to enhance efficiency and productivity. This software acts as the central nervous system of a manufacturing plant, coordinating various processes and ensuring optimal performance. By integrating control software, factories can streamline operations, reduce errors, and improve overall output.
Control software helps in automating repetitive tasks, allowing workers to focus on more complex and strategic activities. It also provides real-time data and analytics, offering insights that drive informed decision-making. In essence, control software is a critical component in achieving lean manufacturing principles.
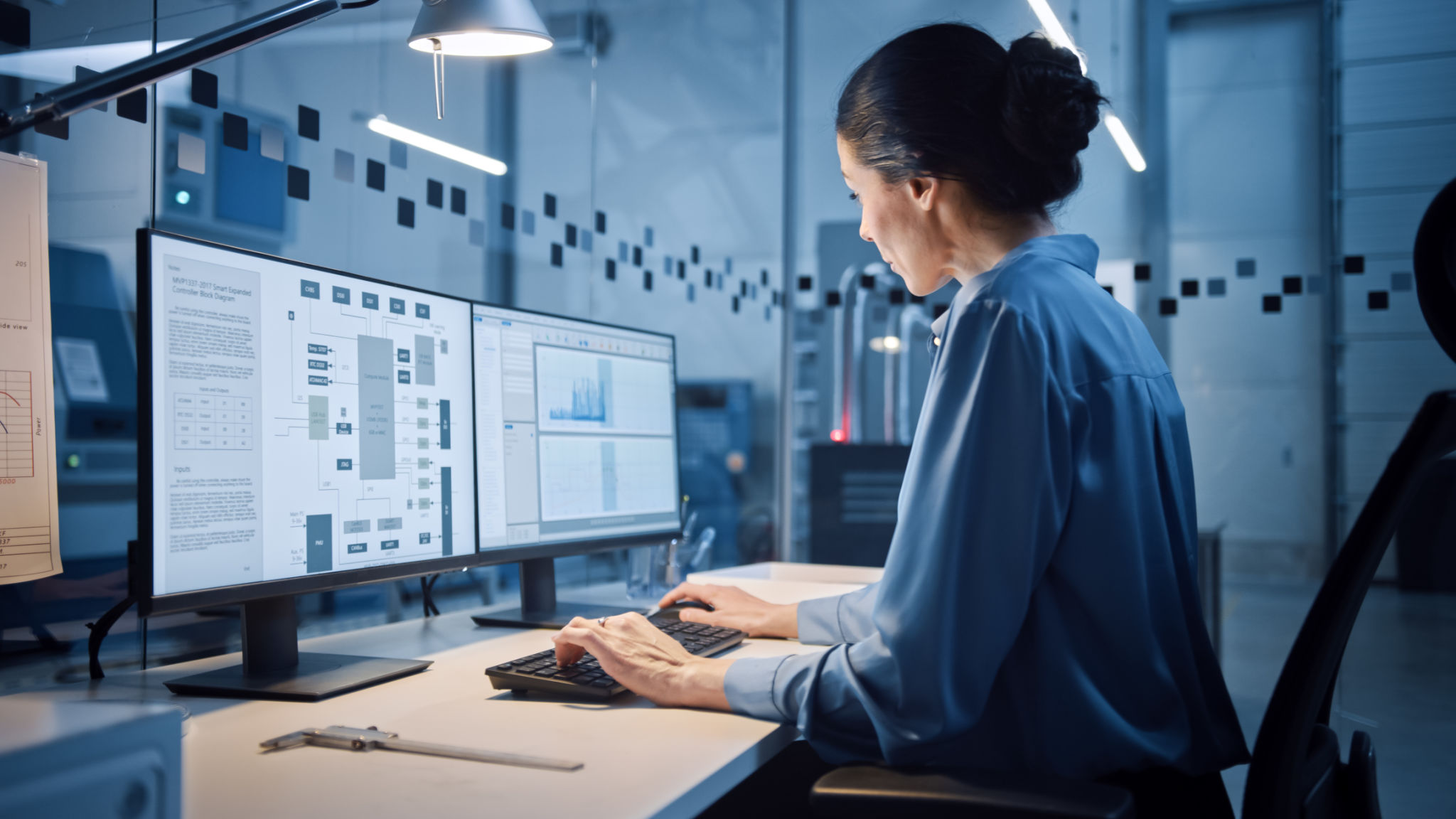
Maximizing Efficiency with Proper Implementation
To fully leverage the benefits of control software, proper implementation is crucial. Start by conducting a thorough assessment of your current processes to identify areas that can be enhanced with automation. Engage with stakeholders across departments to ensure that the software aligns with both operational and business goals.
Furthermore, training is key. Equip your team with the necessary skills to effectively use the software. This not only improves efficiency but also boosts employee morale as they feel more competent and involved in the transition process.
Customizing Software for Specific Needs
One size does not fit all when it comes to control software. Customization is often required to tailor the software to the specific needs of your factory. Work closely with software developers to create modules that address unique challenges within your production line.
Customizable dashboards, for example, allow different departments to focus on metrics that are most relevant to their functions. This promotes a more targeted approach to problem-solving and enhances overall effectiveness.
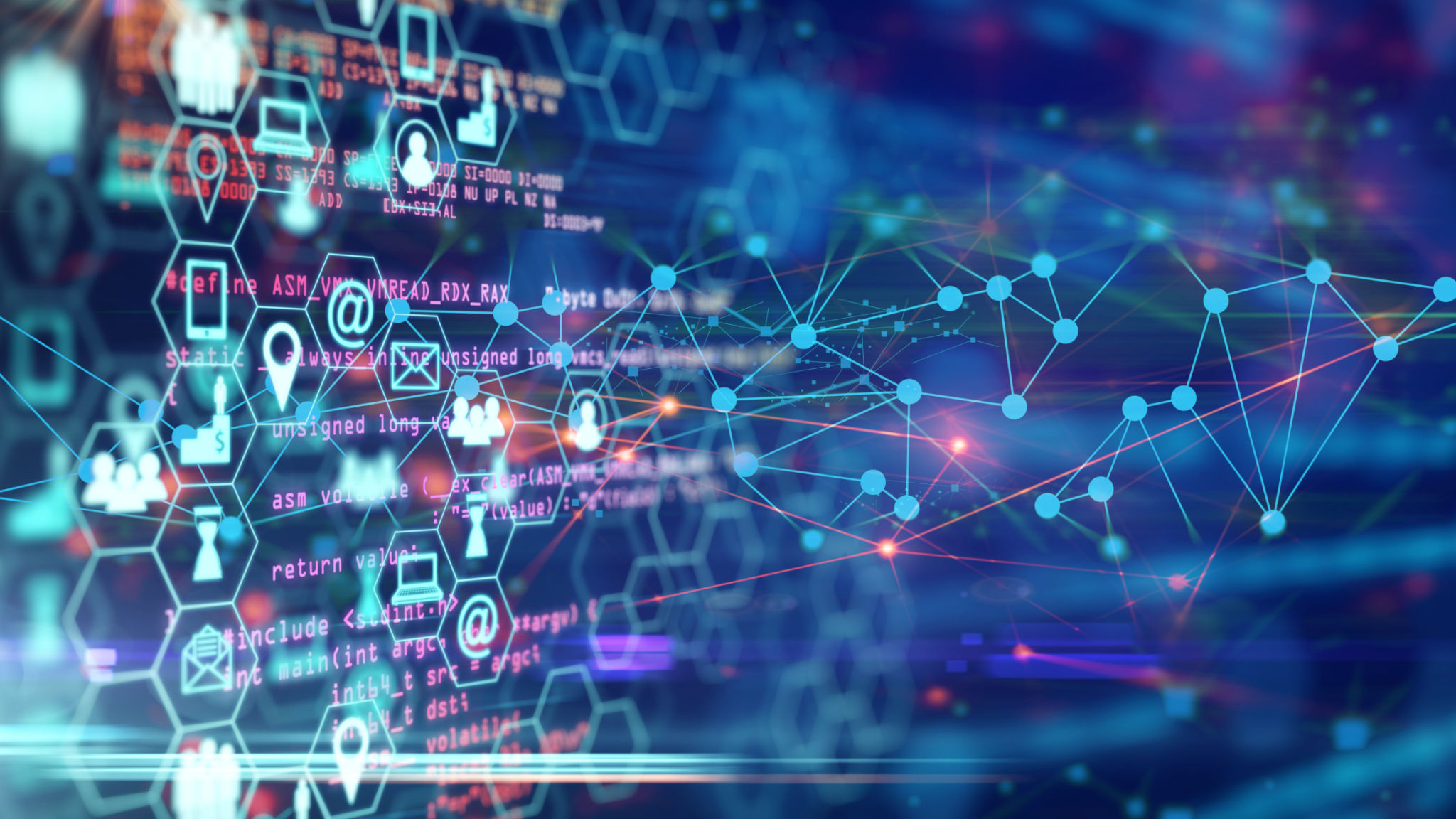
Integrating IoT for Real-Time Monitoring
The Internet of Things (IoT) has revolutionized how factories operate by providing real-time monitoring capabilities. By integrating IoT devices with control software, factories can collect and analyze data from various equipment and processes instantaneously.
This integration allows for predictive maintenance, which can significantly reduce downtime. Instead of reacting to equipment failures, factory managers can proactively address potential issues before they escalate, ensuring continuous operations.
Enhancing Communication and Collaboration
Control software also plays a vital role in enhancing communication and collaboration within a factory. With centralized data accessible to authorized personnel, teams can easily share information and collaborate on projects, regardless of their location.
This seamless flow of information leads to faster problem-solving and more cohesive teamwork. As a result, factories can respond more swiftly to market demands and changes in production requirements.
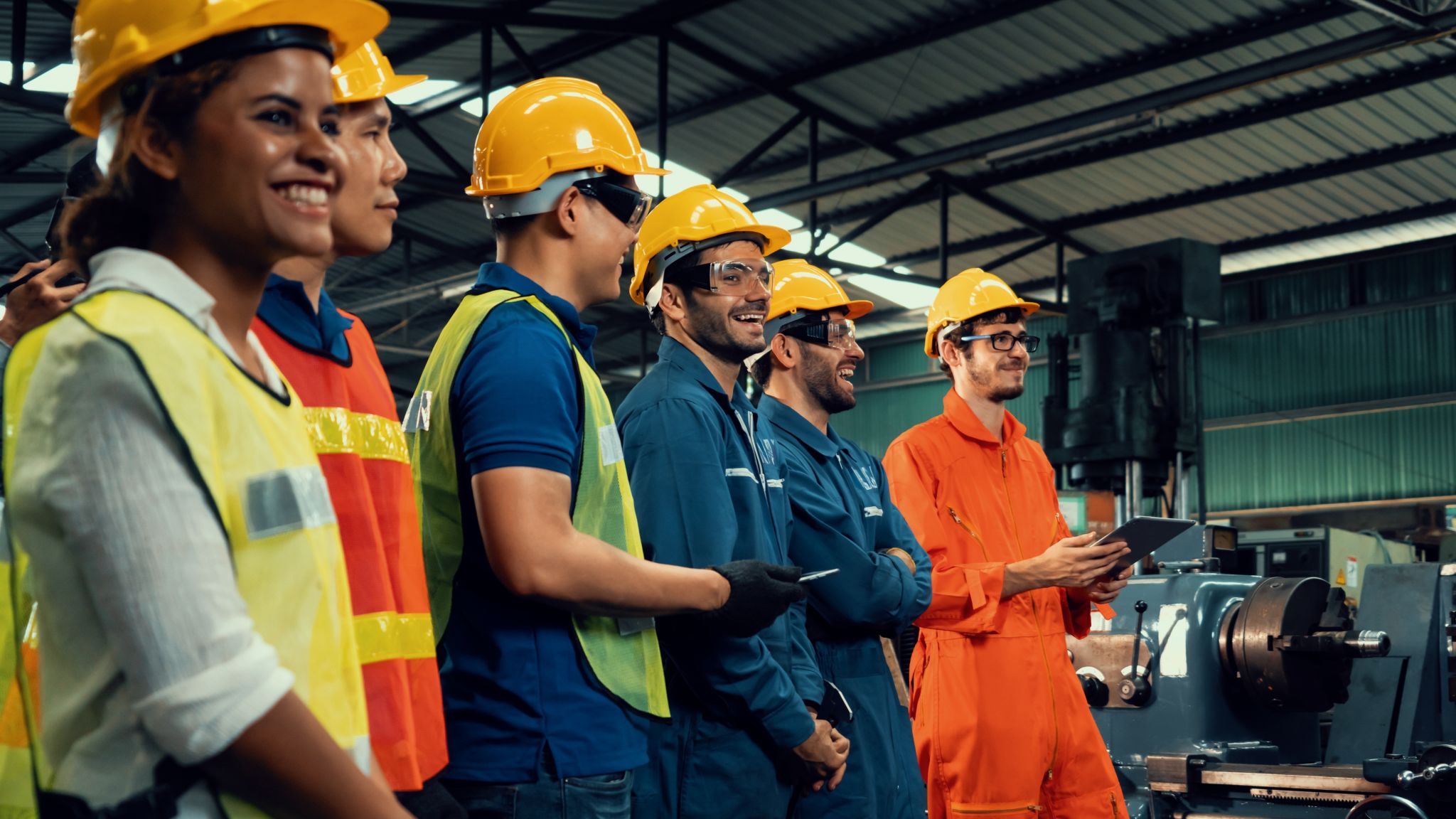
Ensuring Security and Compliance
While implementing control software brings numerous benefits, it is important not to overlook security and compliance considerations. Protecting sensitive data from cyber threats is paramount. Ensure that the software provider adheres to industry standards for security and that regular audits are conducted.
Compliance with regulatory requirements is also essential. Control software should be able to generate reports and documentation that meet industry standards, reducing the risk of non-compliance penalties.
Evaluating Performance Metrics
Finally, regularly evaluate performance metrics to measure the effectiveness of the control software. Use key performance indicators (KPIs) such as production output, error rates, and downtime to assess whether the software meets your factory's goals.
This ongoing evaluation allows for continuous improvement and adaptation to new challenges in the manufacturing environment. By doing so, factories can maintain a competitive edge in an ever-evolving market.