How Advanced Process Control Software Enhances Manufacturing Efficiency
Understanding Advanced Process Control Software
In the rapidly evolving world of manufacturing, staying ahead of the competition requires leveraging cutting-edge technologies. Advanced Process Control (APC) software is one such innovation that has revolutionized the manufacturing sector. Designed to optimize production processes, APC software provides manufacturers with the tools they need to enhance efficiency and quality.
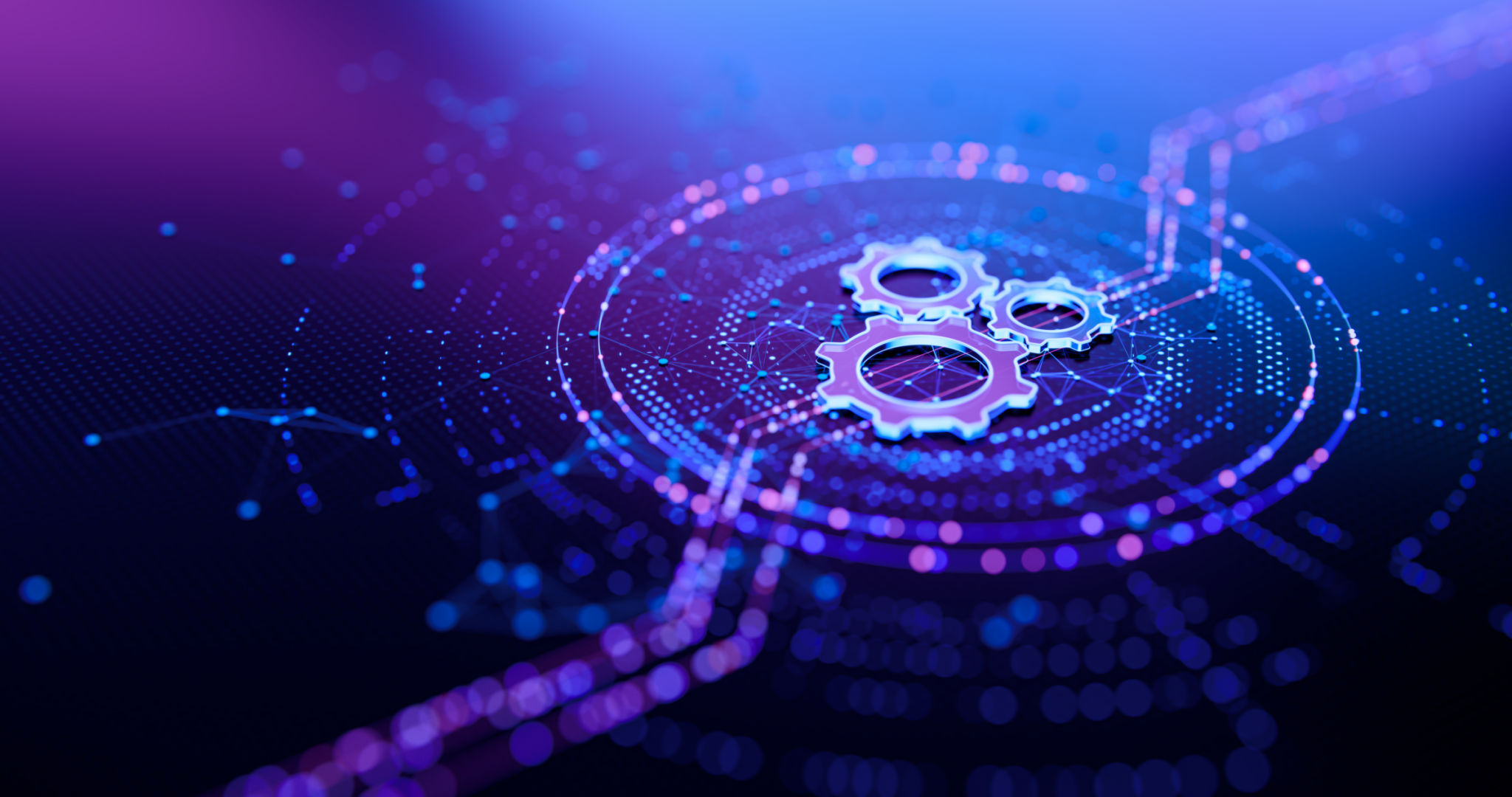
APC software employs complex algorithms and real-time data collection to monitor and adjust manufacturing processes. By analyzing data from multiple sources, it ensures that operations run smoothly and efficiently, reducing wastage and downtime. The implementation of APC can lead to significant improvements in product consistency and throughput.
The Role of Real-Time Data Analysis
A crucial component of APC software is its ability to perform real-time data analysis. This feature allows manufacturers to make informed decisions quickly, responding to any deviations or anomalies in the production line. Real-time data helps in identifying bottlenecks and inefficiencies, enabling swift corrective actions.
With the integration of sensors and IoT devices, APC software can gather vast amounts of data from all stages of the manufacturing process. This data is then analyzed to provide actionable insights, ensuring that the production process remains optimal at all times.
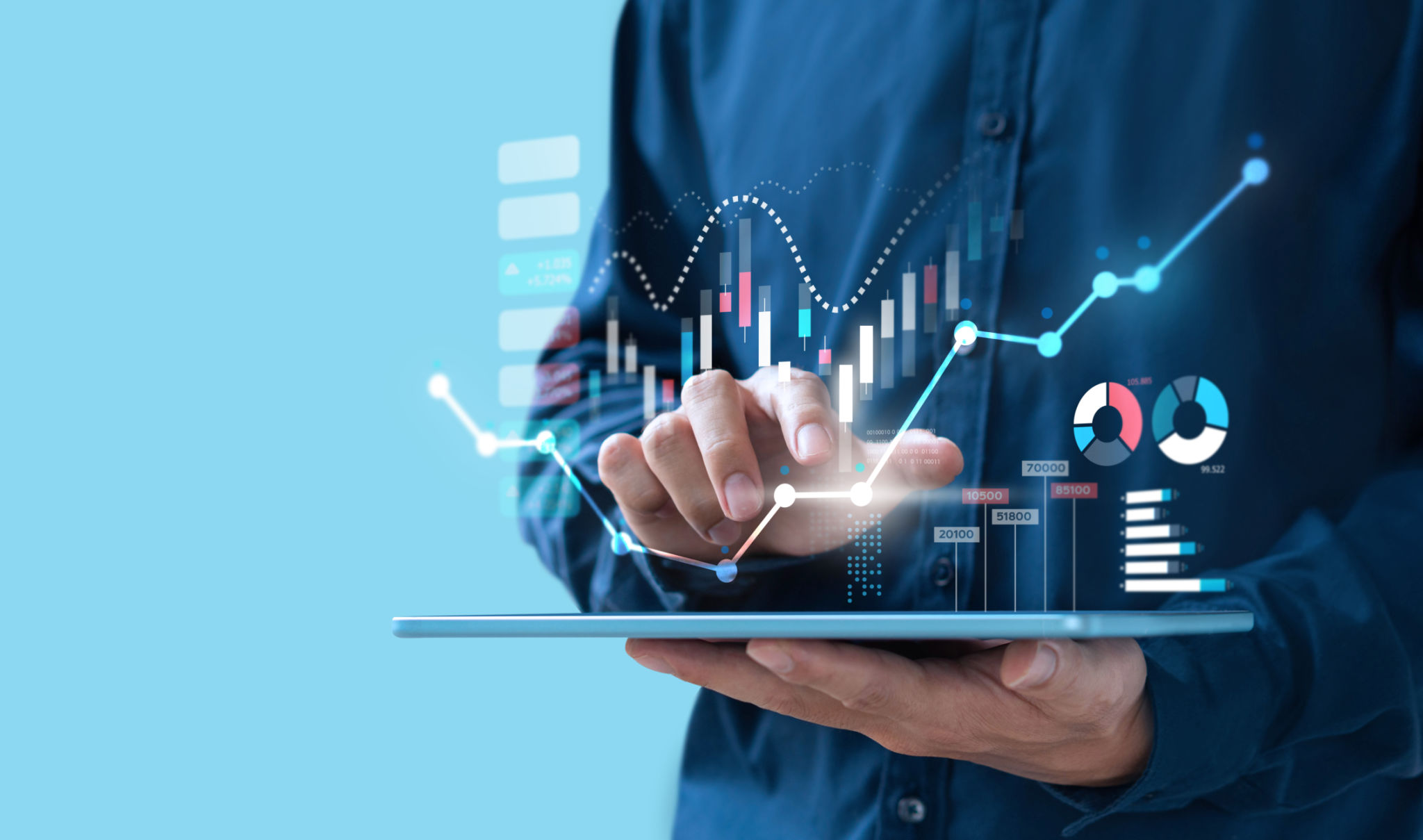
Enhancing Quality Control
Quality control is a critical aspect of manufacturing, and APC software plays a vital role in maintaining high standards. By continuously monitoring production parameters, APC ensures that each product meets predefined specifications. Any deviation is immediately flagged, allowing for quick adjustments to maintain quality.
Moreover, APC software can predict potential quality issues before they occur. Through predictive analytics, manufacturers can anticipate problems and take preventive measures, thus reducing the risk of defects and improving overall product reliability.
Reducing Operational Costs
One of the most significant benefits of implementing APC software is the reduction in operational costs. By optimizing processes and minimizing waste, manufacturers can achieve substantial cost savings. APC software helps in identifying areas where resources are being underutilized or wasted and provides solutions to address these inefficiencies.
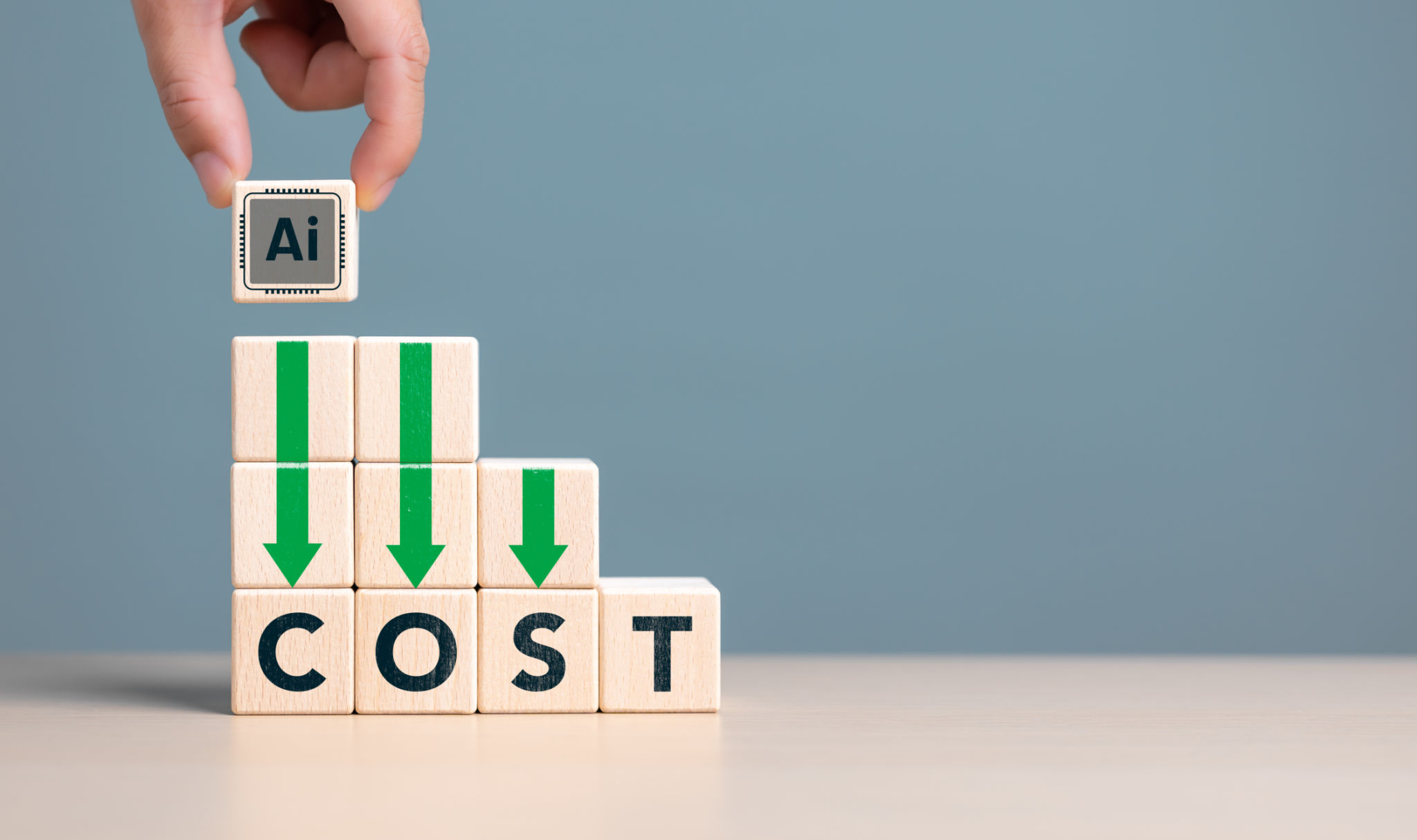
Furthermore, APC enables better resource management by ensuring that machinery operates at peak efficiency. This not only extends the lifespan of equipment but also reduces maintenance costs.
Improving Sustainability
In today's environmentally conscious world, sustainability is a priority for many manufacturers. APC software contributes to sustainability efforts by reducing energy consumption and minimizing waste production. By optimizing processes, it ensures that resources are used efficiently, leading to a smaller carbon footprint.
The ability of APC software to enhance sustainability aligns with global efforts to promote eco-friendly practices in manufacturing. As more companies adopt this technology, it contributes positively to environmental conservation efforts.
The Future of Manufacturing with APC
The future of manufacturing looks promising with the continued advancement of APC technology. As artificial intelligence and machine learning techniques become more integrated into APC systems, their capabilities will only expand. This evolution promises even greater efficiency gains and higher-quality outputs for manufacturers willing to adopt these cutting-edge solutions.

In conclusion, Advanced Process Control software is a game-changer for the manufacturing industry. Its ability to enhance efficiency, reduce costs, improve quality, and promote sustainability makes it an invaluable tool for modern manufacturers looking to stay competitive in an ever-changing market.