Preparing Your Industrial Facility for Seasonal Changes: Process Control Tips
Pe
Understanding the Impact of Seasonal Changes
Seasonal changes can significantly impact industrial facilities, primarily due to fluctuations in temperature, humidity, and weather conditions. These factors can affect machinery performance, product quality, and overall operational efficiency. Therefore, preparing your facility for these changes is crucial to maintain optimal process control and prevent downtime.

Assessing Your Current Systems
Before implementing any new strategies, it's essential to assess your current systems. Conduct a thorough evaluation of your equipment, HVAC systems, and insulation. Look for any signs of wear or potential weaknesses that could be exacerbated by seasonal changes. This assessment will help identify areas needing improvement and ensure your facility is equipped to handle the upcoming season.
Conduct Regular Maintenance
Regular maintenance is a cornerstone of preparing for seasonal transitions. Ensure that all machinery is serviced, lubricated, and calibrated as necessary. This proactive approach helps in avoiding unexpected breakdowns and prolongs the lifespan of equipment. Schedule maintenance activities during the shoulder seasons to minimize disruption.

Optimizing Environmental Controls
Your facility's environmental controls, such as heating, ventilation, and air conditioning (HVAC) systems, play a critical role in maintaining stable conditions. Consider recalibrating these systems to handle the upcoming weather changes. For example, heating settings may need to be increased during colder months to ensure optimal working conditions and prevent machinery from freezing.
Insulation and Sealing
Proper insulation and sealing are vital for maintaining internal temperature stability. Inspect doors, windows, and any other potential entry points for drafts or leaks. Enhancing insulation can lead to significant energy savings and create a more consistent environment for process control.

Adjusting Process Parameters
Seasonal variations may necessitate adjustments in process parameters to maintain product quality. For instance, changes in humidity can affect materials used in production. By closely monitoring these parameters and making necessary tweaks, you can ensure product consistency and avoid waste.
Implementing Advanced Monitoring Systems
Investing in advanced monitoring systems can provide real-time data on environmental conditions within your facility. These systems can alert you to any deviations from desired parameters, allowing for swift corrective action. This technology not only enhances process control but also supports energy efficiency initiatives.
Training and Communication
Finally, ensure your team is well-trained and aware of the changes being implemented. Clear communication about new procedures or adjustments is essential to maintain safety and productivity. Host regular training sessions to keep everyone informed about best practices for handling seasonal changes.
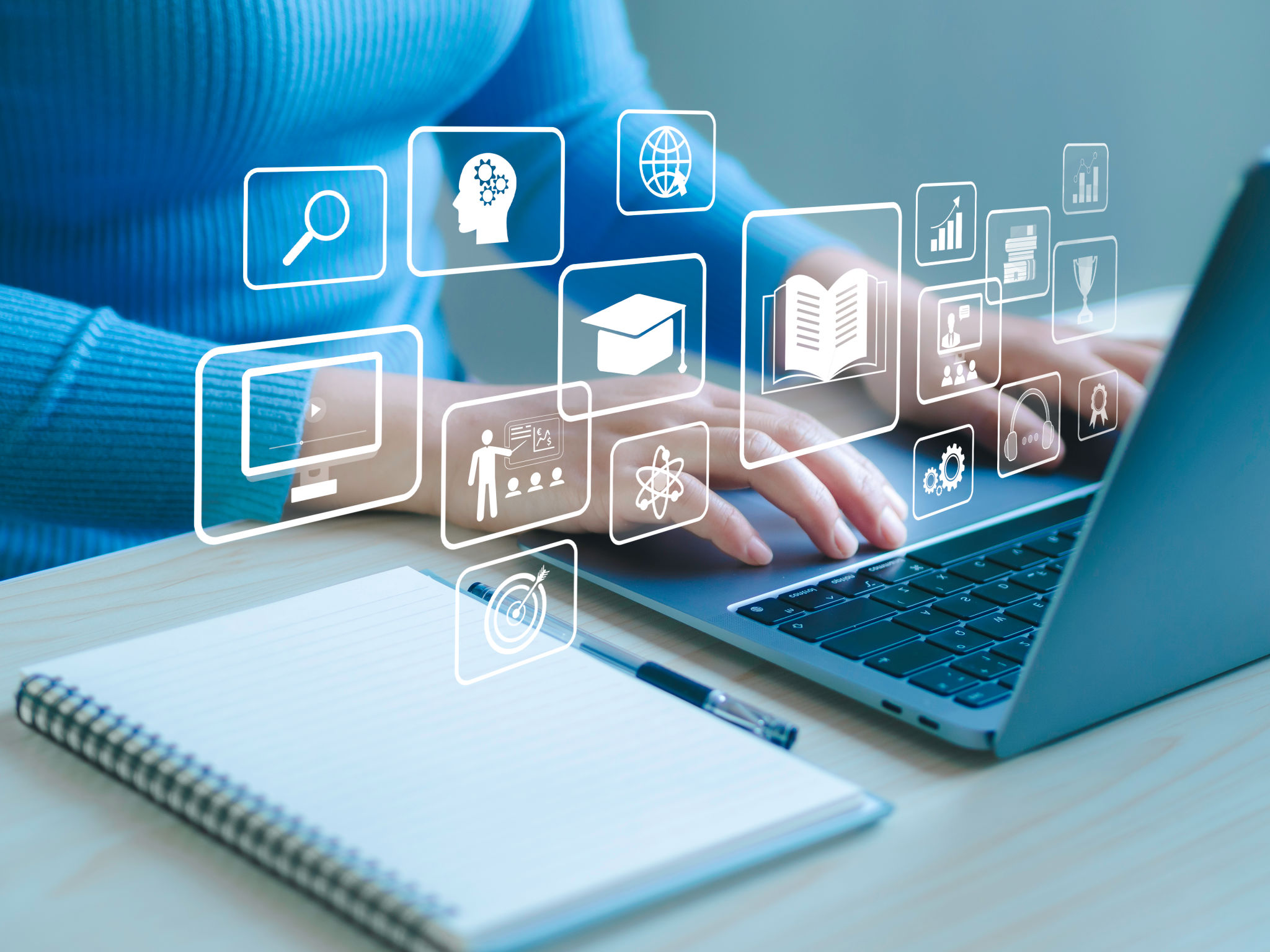
Creating a Response Plan
Developing a response plan for extreme weather events is also crucial. This plan should include protocols for ensuring employee safety, protecting equipment, and maintaining operations during unexpected conditions. Regularly review and update this plan to address any new risks or challenges.
By taking these proactive steps, your industrial facility can efficiently adapt to seasonal changes, ensuring continued productivity and minimizing potential disruptions. Remember, preparation is key to successful process control throughout the year.